Cummings Aerospace ready to manufacture Hellhound munition
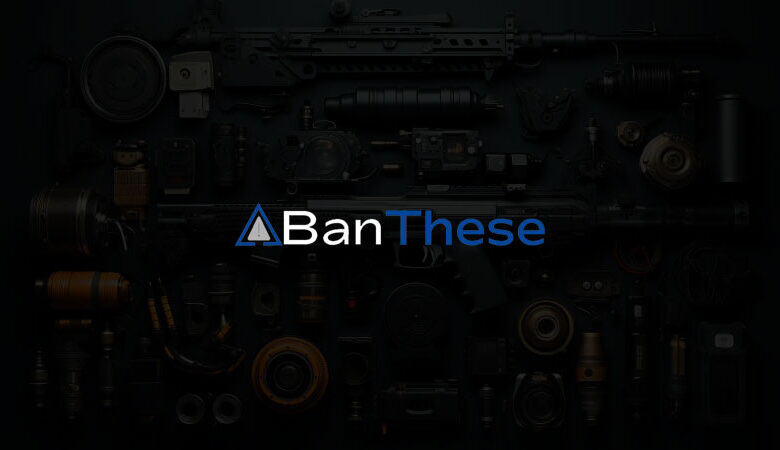
Cummings Aerospace is now ready to manufacture its Hellhound loitering munition at what equates to low-rate production, CEO Sheila Cummings told Defense News in a recent interview at its new production facility near Huntsville, Alabama.
The company chose a space next door to Redstone Arsenal, Alabama, home to the program office and testing and development for Army aviation, in 2021 and designed and built a facility intended to produce large numbers of the drones.
“The work we have done to date, not only with the development of the vehicle, but preparing for major acquisition and production of these vehicles, has been a huge focus for us,” Cummings said. “We’re really excited that we are now at manufacturing readiness level 7.”
The classification equates to a defined production workflow at the facility and the establishment of work instructions for building the air vehicles.
Hellhound, weighing less than 25 pounds, flew faster than 350 miles per hour at full throttle while passing distances of 20 kilometers using just 50% of its fuel, according to the company.
The air vehicle is the first major end-to-end weapon system developed by Cummings Aerospace, a Native American woman-owned small business founded in 2009 as an aerospace engineering outfit with expertise in design, development, production and sustainment of capabilities, including missiles, radars and command-and-control system technologies.
Hellhound will be demonstrated in several upcoming events with special operations, the U.S. Navy and even abroad in the U.K. this summer, according to Cummings.
“We’re using these demo opportunities, in addition to our flight tests, to ultimately execute low-rate production,” Cummings said. “We’re talking about quantities of 12 to 14 vehicles for these demos,” she added, “but it’s really allowing us to fully vet our production process.”
The military is changing the way it acquires weapon systems and, in many cases, requires companies to prove they can build systems at scale as part of competitive acquisitions. Historically, a weapon system might be chosen for its performance on the battlefield without much attention paid to the amount of work it would take to build a system or even how stable the supplier base was.
Cummings Aerospace wrapped up flight tests of its turbo-jet-powered, 3D-printed kamikaze drone earlier this year and is readying the S3 version of its man-portable Hellhound for submission to the U.S. Army’s Low Altitude Stalking and Striking Ordnance, or LASSO, competition set to kick off later this year.
The competition would require the company to build 135 munitions total and would expect companies chosen to build 35 prototypes right out of the gate.
In Cumming’s opinion, the war in Ukraine and tensions in the Indo-Pacific have underscored the need to ensure production capacity and understand the supply chain and its risks.
“That’s what’s driven the whole modular design and making sure that we have an open systems architecture and be able to swap in technologies very readily,” Cummings said.
A large portion of the air vehicle is made using commercially available 3D printers in-house and buying commercially available standard parts that are not unique to just a few suppliers, Cummings said.
“If you think about low-cost solutions — that’s part of the strategy — is we have to design something that we can get screws from multiple vendors, we can get 3D print material from multiple vendors,” she said. “We talk about exquisite payloads, that’s a different challenge, but electronics, we have to make sure we can source them from multiple vendors.”
And to surge even further, Cummings said there are other solutions that are easy to implement like licensing the design to other suppliers to go and produce using standard 3D printers to help expand production capacity.
For the Huntsville facility, Cummings said her goal is to produce at least 100 air vehicles a month.
“Payloads obviously drive some of that,” she noted, but added that there is room to grow beyond that, whether it’s next door or using the supplier base to ramp up demand.
The expectation now is “not just a new, novel technology or capability, but prove that you can make it,” Cummings said. “So we’re proving we can make them and make them at scale.”
Jen Judson is an award-winning journalist covering land warfare for Defense News. She has also worked for Politico and Inside Defense. She holds a Master of Science degree in journalism from Boston University and a Bachelor of Arts degree from Kenyon College.