SILENCER SATURDAY #329: Bring On The Heat – Suppressor Alloy Metallurgy
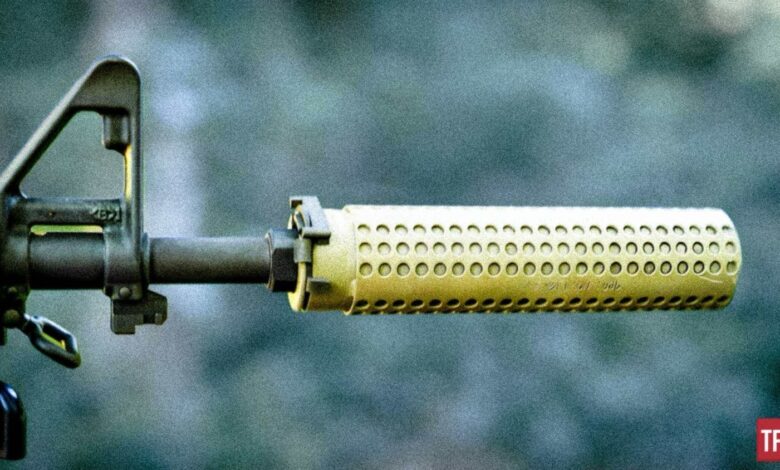
Good afternoon everyone and welcome back to TFB’s Silencer Saturday brought to you by Yankee Hill Machine, manufacturers of the brand new YHM 338 Bad Larry Suppressor. Last week we took a trip back in time to my first suppressor purchase – the 9mm Liberty Mystic. This week we dig in to a bit of alloy metallurgy with a look at the properties of some of the most popular silencer alloys. Should you buy a titanium or steel suppressor? Let’s take a look.
More @ TFB:
SILENCER SATURDAY #233: Full Auto with the Legendary KAC NT4 – USMC Suppressor
Unfortunately, it’s raining here today which means no KAC NT4 burn-down videos. Please report to the den/library for a bit of science.
SILENCER SATURDAY #329: Bring On The Heat – Suppressor Alloy Metallurgy
SILENCER SATURDAY #329: Bring On The Heat – Suppressor Alloy Metallurgy
One common question for first-time buyers usually involves weight, which quickly leads to a discussion about the different types of materials used by manufacturers to build suppressors. And since there is no viable commercial polymer silencer, we are talking about metals. There is some variation in alloys and metal grades, but for the most part, firearm suppressors are constructed using a few different metal alloys or a combination of metal alloys.
Before we dig into the science, here’s my standard disclaimer. I am not a metallurgist, a materials scientist, or an engineer. The information provided in today’s article is broad, generic, and should not be used as a technical resource. If you are building a submarine to visit the Titanic, a spacecraft for a moon mission, or a flame/bullet resistant panic room, use a team of real engineers and references.
Just like in life, everything in the firearm world, and especially the suppressor world, is a compromise. The smallest, lightest platforms are either very expensive to manufacture, or more delicate than their larger, heavier counterparts. Similarly, the toughest suppressors that can handle seemingly endless strings of fire are usually big and heavy. The lightest suppressors are made for low pressure calibers or are not capable of sustained use (usually abuse).
Keeping the term compromise in mind, it is especially important to do a bit of self-introspection to determine your actual needs. If you own select fire weapons or are planning on adding them in the future, investing in a belt-fed rated suppressor may actually be on your list of requirements. Otherwise, you may end up with a heavier, more expensive silencer that will never endure it’s designed extreme environmental limits.
Outside of rimfire models, most suppressors are constructed with one or more of three alloys: steel, nickel, or titanium. Each one has certain characteristics that make them the preferred choice for firearms applications, including strength, heat resistance, machinability, corrosion/chemical resistance, and availability.
As a basic scientific principle, an alloy is a substance that is made by combining to or more metals to achieve a specific characteristic or property. Let’s take a look at the four most common metal alloys used in the firearms industry.
17-4 Stainless Steel
Possibly the most common alloy used in the gun world is stainless steel, an iron-based alloy that is formulated to resist corrosion amongst other traits. As metal alloys go, it is relatively inexpensive and available from a wide variety of suppliers. A high tensile strength rating over a longer, more linear temperature range.
- Carbon: 0.070 Max
- Chromium: 15.0-17.50
- Columbian + Tantalum: 0.15-0.45
- Copper: 3.00-5.00
- Manganese: 1.00 Max
- Nickel: 3.00-5.00
- Phosphorus: 0.040 Max
- Silicon: 1.00 Max
- Sulfur: 0.030 Max
- Iron: Balance
Properties:
- Temperature (Max): 600 deg F
- Tensile Strength: 190,000 psi
Source: Progressive Alloy
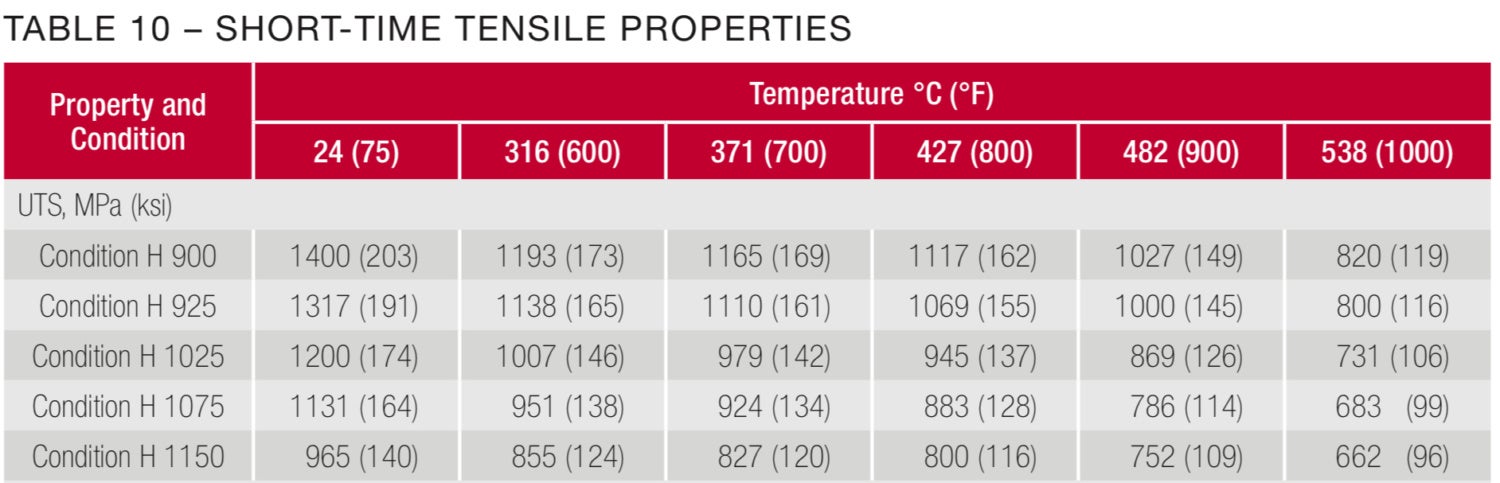
Credit: aksteel.nl
Note: To convert ksi to psi the multiply the value by 1000. Example: Condition H 925 has a tensile strength of 191,000 psi at 75 deg F and 116,000 psi at 1000 deg F (second row).
INCONEL 718
INCONEL is a registered trademark of the Special Metals Corporation and is a metal alloy comprised of about 50% Nickel. Known for it’s strength at high temperature, INCONEL and other nickel alloys have relatively flat yield and tensile strength curves until temperatures reach about 1400 deg F.
- Nickel (plus Cobalt): 50.00-55.00
- Chromium: 17.00-21.00
- Iron: Balance
- Niobium (plus Tantalum): 4.75-5.50
- Molybdenum: 2.80-3.30
- Titanium: 0.65-1.15
- Aluminum: 0.20-0.80
- Cobalt: 1.00 max.
- Carbon: 0.08 max.
- Manganese: 0.35 max.
- Silicon: 0.35 max.
- Phosphorus: 0.015 max.
- Sulfur: 0.015 max.
- Boron:0.006 max.
- Copper: 0.30 max
Properties:
- Temperature (Max): 1300 deg
- Tensile Strength: 150,000 psi
Source: Special Metals
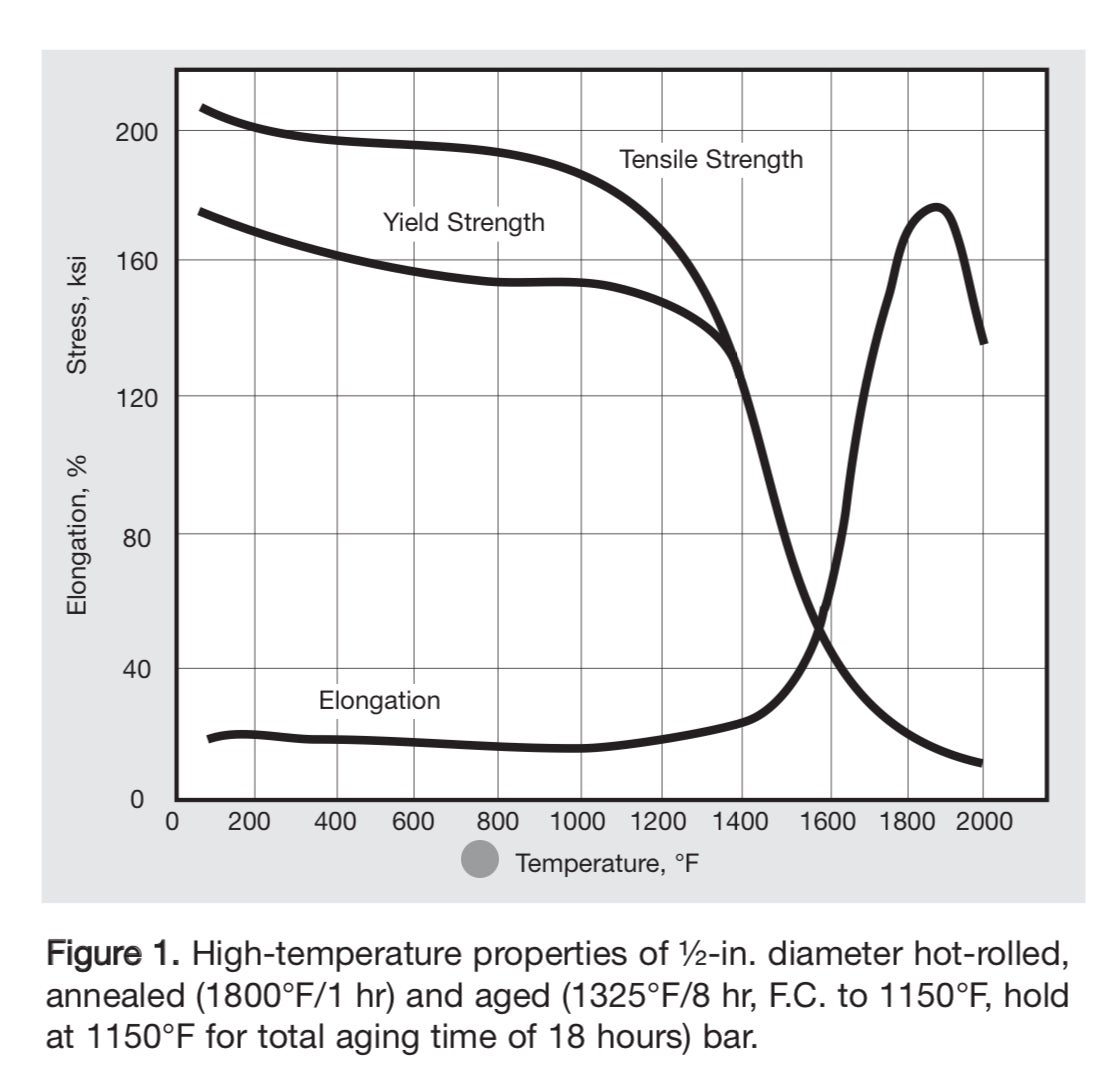
Credit: Special Metals
Titanium 6AL-4V
Titanium alloys are known for high strength to weight ratios with weights comparable to aluminum alloys and strengths comparable to some steel alloys. The catch is that yield and tensile strengths immediately start to decline as temperatures rise. By the time it hits 600 deg F, tensile strengths can fall below the strength of some aluminum alloys.
- Temperature (Max): 660 deg F
- Tensile Strength: 160,000 PSI
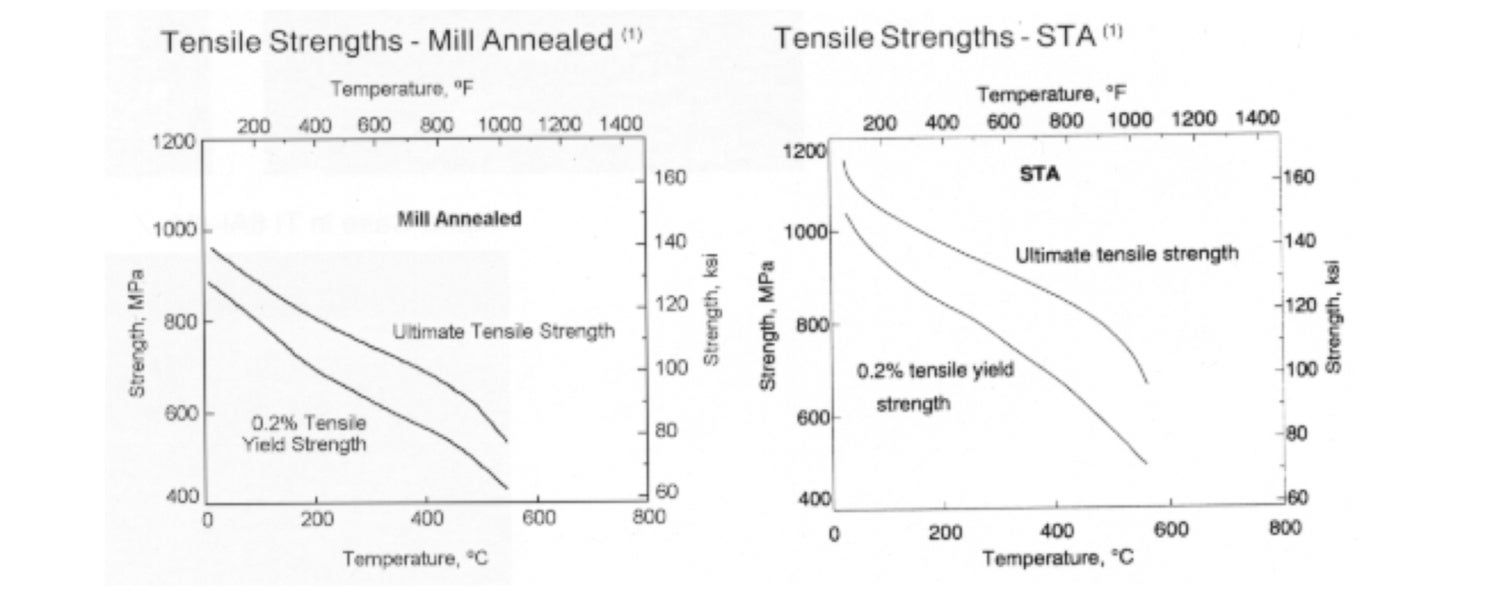
Credit: Carpenter Technology
Source: Carpenter Technology
7075 Aluminium
Aluminum alloys are light, inexpensive, and easy to machine. Unfortunately tensile strengths dive to critical levels around 250 deg F.
- Zinc: 5.6 – 6.1%
- Magnesium: 2.1-2.5%
- Copper: 1.2-1.6%
- Aluminum: Balance
Properties:
- Temperature (Max): 212
- Tensile Strength: 83,000
Source: alro.com; matweb.com
Besides the composition of metal alloys, the heat treating process can play a large part in the strength ratings, especially at elevated temperatures. Suppressor manufacturers sometimes post the specific alloy used in manufacturing, but I have yet to see the specifics on the heat treating processes used by the suppliers. For proper metallurgical reactions to take place (the precipitation phase), annealing temperatures, cooling temperatures, and aging times must be followed. For example, INCONEL has two recognized annealing processes:
- Solution anneal at 1700-1850°F followed by rapid cooling, usually in water, plus precipitation hardening at 1325°F for 8 hours, furnace cool to 1150°F, hold at 1150°F for a total aging time of 18 hours, followed by air cooling.
- Solution anneal at 1900-1950°F followed by rapid cooling, usually in water, plus precipitation hardening at 1400°F for 10 hours, furnace cool to 1200°F, hold at 1200°F for a total aging time of 20 hours, followed by air cooling.
There are more exotic alloys in use, notably the C300 Maraging nickel-cobalt superalloy from our friends at Energetic Armament, makers of the VOX-S. They even have a graph comparing the tensile strength of common alloys at certain temperatures. C300 starts at 275,000 psi!
There is obviously a lot more to discuss when it comes to common suppressor alloys, strength ratings, and temperature resistance, but this gives you a little extra knowledge when reading manufacturer’s specifications and hopefully make more informed decisions.
When it comes down to it, short barrels and heavy rates of fire deserve stainless steel, INCONEL, or other high performing alloys. If weight is a concern and higher rates of fire are not anticipated, a titanium suppressor is probably a better choice.
Thanks for reading. Be safe, have fun, and we’ll see you back here next week for another Silencer Saturday.